SUSTAINABILITY
Sustainable steel production? Volvo and Daimler invest
A great deal of automotive ESG initiatives are currently focused on reducing the sector’s greenhouse gas emissions by electrifying the vehicle fleet, but that only goes part of the way to reducing the industry’s totally greenhouse gas emissions
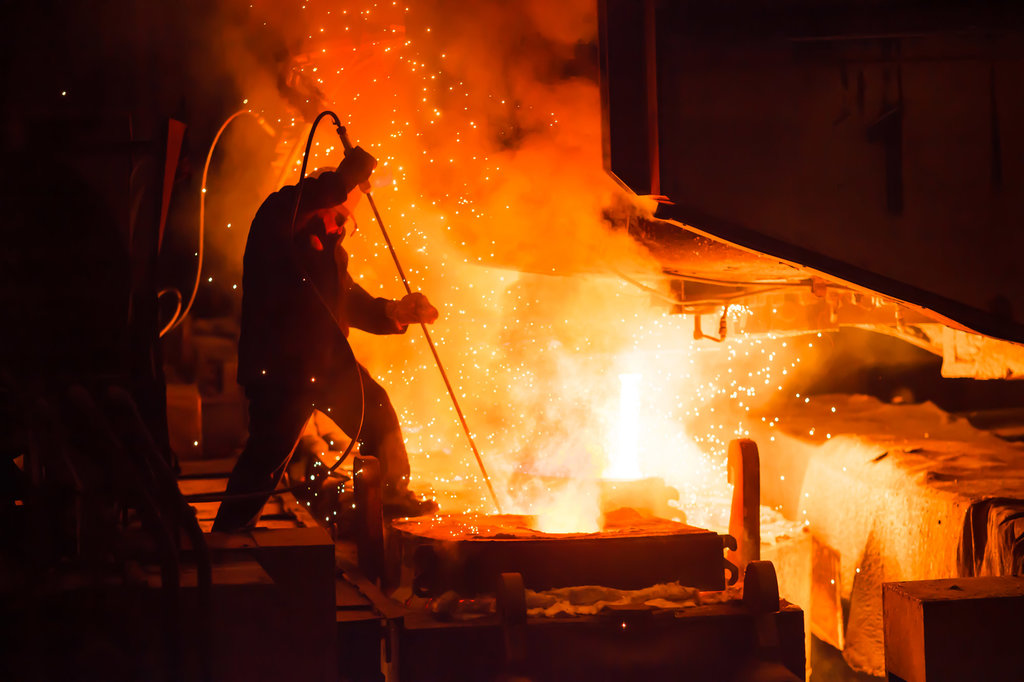
E
Vs may come with clean powertrains that do not burn fossil fuels, but they are likely to still be made from steel and aluminium products – the production of which is a significant contributor to the industry’s total emissions.
However, a new development by Swedish steelmaker SSAB in collaboration with ore producer LKAB and energy company Vattenfall, has led to what is claimed to be the world’s first ‘fossil-free steel’ using its ‘Hybrit’ process. This aims to stop the use of fossil fuels in steelmaking in two different ways.
Steel is made from iron that has been smelted from ore by removing oxygen.SSAB’s approach eliminates the coal and coke from this process, using hydrogen instead to reduce oxygen content, enabling it to be processed into steel – producing water as an emission rather than CO2. That hydrogen is, itself, produced using electrolysis powered by renewable energy, removing the carbon emissions common to non-green hydrogen sources. The hydrogen also acts as an energy store to account for the fluctuating output of renewable energy sources.
The second significant source of greenhouse gas emissions in steelmaking is in generating the power needed to heat the furnaces to thousands of degrees Celsius. Traditionally, blast furnaces powered by fossil fuels would be employed to make steel, using tremendous amounts of power and producing vast amounts of emissions in the process. SSAB has committed to replacing all the blast furnaces it operates with electric arc furnaces, which perform the same task but powered by renewable energy rather than fossil fuels.
Volvo was confirmed by SSAB as the first customer to receive fossil-free steel for evaluation. SSAB claimed in June 2021 that it had already produced 100 tons of fossil-free steel in Sweden and was preparing to roll the process out to the rest of its production network in Northern Europe over the next two decades.
Using the Hybrit method, SSAB believes that the total carbon dioxide emissions for the whole of Sweden could be reduced by 10% and Finland’s by 7%.
By 2026, SSAB says it will be offering fossil-free steel at a commercial level and will have converted the furnaces at its Oxelösund, Sweden factory to electric arc variants. SSAB notes that the ‘Hybrit’ steelmaking method does cost more than traditional steelmaking methods and, as such, the steel produced will cost more to supply – however, auto customers such as Volvo will be weighing up the extra financial cost of fossil-free steel versus the ESG costs of continuing to use steel with carbon emissions attached.
Already, Faurecia and Daimler have expressed interest in the process, with the latter launching a partnership with SSAB in September 2021 for fossil-free steel. The German auto giant noted that it expects its new car fleet by 2039 to be completely carbon neutral, along with the entire value chain that supplies it.
Daimler has also decided to deliberately pursue direct reduction of carbon emissions, rather than the offsetting of those emissions through compensation schemes. This can be considered a more sustainable long-term approach to truly reducing greenhouse gas emissions.
Of course, cars are not only made from steel. Many make use of large amounts of aluminium in their construction, which comes with its own associated emissions costs. BMW has already begun planning the reduction of emissions from this source and has signed a contract worth at least €100m with Emirates Global Aluminium (EGA), for 43,000 tons of aluminium supply through 2021.
EGA’s method sees it generate the energy to refine aluminium using a vast solar farm in the Dubai desert – planned to become the largest of its kind in the world. BMW says this move will reduce its total CO2 emissions by around 2.5m tons by 2030 – or by roughly 20% across its entire supply chain.